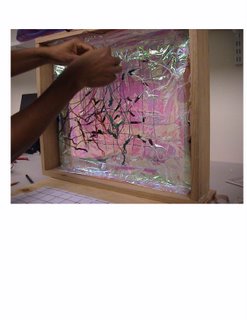
Shape Memory Wire Experimentation
By Dido Tsigaridi & Mikael Powell
Since the early 1930’s researchers have observed an unusual temperature activated shape-changing phenomenon in various alloys. While the effect seemed hopeful to provide physical movement for machinery, the metals themselves proved problematic for mass application. Early alloys were either too expensive or too toxic. Modern researchers continue to test alloys in regards to their efficacy and unique transformation characteristics. Our particular interest is not in the metallurgy, but rather, the variables inherent in the shape-changing phenomenon. We will therefore review the material specifications and qualities used in our research, test the variables and offer concluding remarks.
MATERIALS USED FOR OUR EXPERIMENTS
Shape memory alloys are materials whose microstructure changes with an input of thermal energy. Although the phenomenological result may suggest that shape memory materials are energy-exchanging, they are actually property-changing.[1] Thermal energy is not transformed into kinetic energy, as one may think by observation. Heat enables an alteration of the material’s microstructure through a crystalline phase change.
The material we used for our experimentation is NiTi (Nickel and Titanium alloy). NiTi can be temperature-activated by direct heat or through resistance to electrical current. Quite simply, the material is “programmable” at very high temperatures and formable when cooled. Upon returning to its warm, resilient state, it "remembers" its programmed shape and returns to it - applying force against anything it its way.[2] Moreover, the manufacturer purports that NiTi is very resilient, lightweight, non-corrosive, biocompatible and wear resistant. Many engineers specify nickel titanium for two qualities: shape memory and super-elasticity.[3] These two characteristics distinguished NiTi from ordinary metal blends in their first scientific publication of 1963.[4] For our experimentation three different shape memory alloy types were used. They are bar shape, electric piston assemblies and NiTinol wire of circular cross section. Their specifications are as follows:
a. Bar Shape #SMA-5A, 0.023” x 0.074” x 5”, by Shape Memory Applications, Inc.
It is a Nickel-Titanium Alloy (Ni -55.5%, Ti -Remainder, Fe -0.05% max., C -0.05%max., H -0.05% max., other trace elements <0.01h0.005 title="" style="mso-footnote-id: ftn5" href="http://www.blogger.com/post-edit.g?blogID=17188973&postID=113942546002516422#_ftn5" name="_ftnref5">[5]
b. Electric Piston by Mondo-tronics Inc.
It is an all-electric linear actuator shape memory wire mechanism that shortens in length with great strength and speed. Its optimum voltage is at 4.5V.
c. HS-6 Nitinol Memory Wire, 0.0297” diameter, by Educational Innovations Inc.
It is a Nickel-Titanium Alloy with a transition temperature between 30oC and 50oC. Its optimum voltage is at 9V. The temperature required to “set” a new shape is 500oC.
QUALITIES OF THE MATERIAL
Shape memory is a design function of the material's temperature. Nickel titanium undergoes a phase transformation, as the material is heated or cooled through its temperature transition range. A NiTi spring with a transition temperature of 42 o C reacts like a typical spring above this temperature in its austenitic state and is flaccid in its martensitic phase below 42 o C. It recovers its shape with significant forces if the temperature rises above 42 o C. It is important to mention that the temperature at which the phase transformation occurs is adjustable over a wide range. Thus, it can be adjusted to approximate body temperature or even extremes in excess of 150oC or below -100 o C.[6] NiTi wires respond to a temperature range of -25oC to 75oC.
The manufacturing process starts with the alloy being heated to 500oC (or much more for specific alloys) which aligns the atoms into a compact and regular pattern. Workers can form the alloy into the desired shape using many standard metallurgic techniques (i.e. cold forming). NiTi manufacturing is more complex because titanium is very reactive. An inert environment is needed to melt the material and similarly heat-joining methods are problematic. Cold working provides a very fine-grained material, which allows for the manufacture of fine wire.
Super-elasticity describes the material's ability to recover from large amounts of strain. A NiTi component can fully recover from strain values up to 8%. Stainless steel, by comparison, will withstand only 2% strain. The super-elasticity of NiTi allows it to perform functions that would permanently deform other materials.
VARIABLES STUDIED IN THE FIRST STAGE OF EXPERIMENTATION
As a first step in our bibliographical research and experimentation with the shape memory alloy, we tried to identify the different variables which influence the phenomenological effects of ‘memory’ and ‘movement’. Being aware that the variables for the transformation of shape memory alloys from the martensite to the austenite structure are numerous, we selected to focus only on five parameters and examine the field of their influence.[7]
“Temperature influences the shape and the speed”
The fact that these materials change in relation to temperature is a characteristic attributed by default to this category. Thus, our experiment investigates the way temperature influences the speed with which the shape transformation takes place.
Experiment 1 – Shape Memory wire electric pistons- researching voltage to reaction time. In this research, we used a component spring assembly. The electric pistons are 8.5 cm long when the interior SMA spring is in the fully extended martensitic position. A standard exterior overforce spring extends to protect the device from overstrain. The austenite state of the alloy wire is pre-designed for the spring to be 6.2 cm in the contracted position. The spring remains pliable below the activation temperature. The energy changing process is actuated by heat generated by electric current.
One end of the piston is fixed to the wall and the slider is deformed to a specific length. Six trials were conducted, each with a different voltage to the piston. Time is calculated from application of current to slider return to the first position. (Please see Exhibit 2 in Video Appendix).
In conclusion, we found that the action required 50:04 seconds with a 3 Volt charge; 18:22 seconds with 4.5 Volts; 17:20 seconds with 6 Volts; 16:05 seconds with 7.5 Volts and 15:11 seconds with 9 Volts. In testing heat to reaction time, please note that there is a dramatic difference between the length of reaction time and voltage at 3 volts and 4.5 volts, but beyond those levels the deviation is minimal through our maximum voltage of 9 volts. The relation between voltage and speed is not linear. (See Exhibit A)
“The wire diameter influences the minimum bend radius and the force released”.
Minimum bend radius describes the smallest bend a wire can make without risking damage. Sharp bends or kinks should be avoided because they can overstrain and weaken the wire. As a rule, a wire should not be bent tighter than fifty times its diameter. The following table shows the linear relation (inversely proportional) between wire diameter and minimum bend radius for some common wires (See Exhibit B). Thus, the thicker the wire, the less it can be bent.
In addition, the force produced by shape memory wires when moving from a martensite to an austenite phase is related to the wire diameter. For greater strength devices may use many wires in parallel. The following table shows the forces generated by groups of wires of various sizes, as well as how much weight they can lift and the total power needed to activate them (See Exhibit C). [8]“Application of heat affects reaction speed and fatigue”
The property-changing phenomenon does not occur at a uniform rate. After heat is applied in the martenistic state, there is a distinct series of reaction rates. Older experimentations show that transformation starts with a small speed, then accelerates and is finally accomplished slowly (See Exhibit 10 in Video Appendix)[9]. Although numerical data was not collected in order to document this observation, it is worth remembering that speed is not independent from the time that heat is applied to the shape memory wires. Fatigue is a complicated issue that occurs from a variety of reasons.[10] Educational Innovations Inc. instructional literature states “do not heat the wire more than is necessary to release the tension”. From our experience, the wire needs to cool right after its transformation from martensite to austenite phase. Heating longer while restraining its movement may cause “training” to a new shape even if the heat was not at the normally required level.
“Selective zone heating influences the speed and the trajectory”.
Many manufacturers of shape memory wires propose activating the material with a hairdryer or a pot of hot water. They assume that the wire should be uniformly heated for maximum effect. (Please see Exhibit 1 in Video Appendix). Our experience has informed us that heating particular zones of the wire exhibit different effects.
Speed is highly influenced by the point of heat application. We noticed that if a straight wire with a bend in the middle were heated close to the bend, it would immediately go back to its straight position. If voltage is exerted to its edges, away from the bend, it will take much more time to go back, or it may never reach the austenite shape. With this in mind, we did some experimentation to explore the trajectory a wire follows going from shape ‘A’ to shape ‘B’. We selectively applied heat to zones along the wire. Also, we introduced an additional parameter to our experiments: one fixed point. We tested the wires with a fixed point in the middle and on the end.
Experiment 2 - 2D Selective zone heating – Mode I - Graphically charting path of the ends and intermediate points with fixed end point. Many experiments have been conducted with uniform heating. For this experiment we wanted to study selective heating. The Nickel-Titanium alloy bar stock was pre-set in the austenite state to be linear. A 7 ½” length was deformed in the martensitic state to have two opposing radius bends. Direct heat application was used.
We constructed a neutral background to accept the travel indication. Different colored acrylic paints were applied to the SMA wire at each endpoint and the centerline of the radius. For Mode I, the end point was fixed to the background. Heat at 204 degree C (400 degree F) was directly applied systematically to each zone. We charted the path of the points along the shape to the austenite conclusion. (Please see Exhibit 3 in Video Appendix)
In conclusion, we noted that selective heating changes the trajectory of points along the shape as well as the culminating shape. The order of heat application determined the distinct route of each point. Also, heat application near the fixed end of the wire substantially effected the movement at the opposite unfixed endpoint. The length of path is greater the farther the point is from the fixed end. The zone heating method allows the wire to maintain both martensitic and austenitic states contiguously. (Please see Exhibits D -G)
Experiment 3 - 2D Selective zone heating – Mode II -Graphically charting path of the ends and intermediate points with fixed center point. This experiment was similar in scope to the preceding one except the center point (in lieu of the end point) was fixed to the background. (Please see Exhibit 4 in Video Appendix). We noted that the closer the heat application to the fixed center point, the less erratic the path and distance of the point movement. Also, as with the previous experiment, the order of heat application determined the distinct route of point. (Please see Exhibits H -K)
“Re-set ability is dependant on an external or counterbalanced force”.
Apart from the one-way shape memory wires (to which we refer in this paper as SMW) there exist also the two-way shape memory alloys (TWSM). In the TWSM change occurs upon both heating and cooling. In the cooler temperature, a TWSM can be easily deformed from a state ‘A’ to a state ‘B’. When heat is applied, the TWSM goes back to state ‘A’, similar to a simple SMW. After cooling again though, it “remembers” the ‘B’ state and returns to it.[11] Since we did not use TWSM in our experiments, we examined different ways that a SMW can acquire a re-set ability.
The obvious solution to have re-set is to apply an external force. In our experiments this would mean either to deform again a wire by hand or to pull a piston. However, we were more interested in finding a way to create a counterbalanced force, which would act automatically and would re-deform the shape memory material. We tested this in two different experiments.
The first experiment involved pistons, which were alternately activated to reset the action. Two electric pistons (all-electric linear actuator SMW mechanisms) and a 25w, 120v 60Hz device were used. The pistons were connected together and systematically activated at 7.5 volts. When voltage was exerted to the deformed one, it was going back to its primary position by pulling (deforming) the other at the same time. (Please see Exhibit 5 in Video Appendix)
The second experiment used the same principal but, instead of two pistons, one piston and a weight created the system. A balanced mechanism was produced. Each time current was exerted to the piston, it raised a piece of steel. When the current was off, the steel pulled back the piston because of its weight.[12] (Please see Exhibit 6 in Video Appendix)
In conclusion, we should mention that a system can be alternately activated to reset an action. Many SMA components need to be reset to their first state by mechanical means. I is usually a bigger and inelegant action. Our effort was to lead this part of our research in a path where the reset phenomenon could be developed to allow for a self-perpetuating cycle without adding many mechanical parts.
THE SECOND STAGE OF EXPERIMENTATION
For this series, we built upon our previous experimentation with shape memory wires. Previously we studied the variables such as time, heat, bend radius, zone heating and reset ability. This time, however, we are confining our research to the variable of direct heat to various zones of the wire to experience phenomenon in three dimensions. Our final project is not an object; rather it is an armature to support different applications and their distinct properties.
After reviewing our previous experimentation and research, we compiled the following chart to illustrate the variables employed in our final project. This table shows the interplay between fixed parameters and both independent and dependant variables in the new equation we established.
The temperature transferred to the wires is fixed and produced by a 12 Volt current. The diameter of the wires used was chosen to be 0.0297” so as to be thin enough for tight bents, but thick enough for high force. The heat application time is an independent variable which will change upon the user’s wish. The reset ability will be established either by an external force or by a self-deformation generated according to the heat application time (dependant variable). Finally, selective zone heating is meant to be another independent variable. The zones of heating will be pre-selected, but the way of their alteration for the production of the effect will be manipulated by the user.
For the final project we moved from the single shape memory wire, and the 2D plane of its movement, to a net of wires, and the 3D plane accordingly. Three experiments were carried out before moving to our final step. The first experiment considers all the new variables, but is still in a 2D plane, while the next two are in 3D. A difference between the 2D and 3D experiments lies in the fact that the 3D tests do not have any fixed points. The wires are free to move in a floating surface and restraining forces are exerted only because of the friction or the weight of the system. In contrast, in the 2D experiment each wire of the parallel system of wires has one edge fixed, as described below.
First Prototype -2D Selective zone heating (heat applied linear array to manipulate fabric sculpture)
The nickel-titanium alloy (Nitinol) wires (.0297” d.) were pre-set in the austenite state to be linear. Six 12” long wires were deformed in the martensitic state to have five alternating 1” d. radius bends each. Direct heat application was then used alternatively in the different bents to create a visual effect. (Please see Exhibit L, M)
More precisely, a wood frame was created to accommodate the wires. The wires were put in a series. A synthetic yarn woven fabric shroud was placed over the wire assembly. A 25w 120v 60Hz device was used to apply heat which was directly applied randomly to each zone of the wires.
As a result of this procedure, we noted that selective heating in random sequences reformed the shape of the fabric in various ways, through different speeds and in a variety of angles. The gentle visual three-dimensional effect produced, resulted only by transformations of the wires in six XY planes. (Please see Exhibits N - O)
First Prototype - 3D Uniform heating (SMW grid woven through cotton fabric)
The nickel-titanium alloy (Nitinol) wires (.0297” d.) were again pre-set in the austenite state to be linear. Eight 8” long wires were configured in a grid pattern and adhered to a gauze sheet approximately 9” wide by 9” long. The gauze was able to move freely in the table and the only force applied to it was the one of its own weight.
More precisely, the shape memory grid (XY), which was attached to the gauze, was bent in the Z axis so as to create an uneven surface. A hair dryer was then used to bring the system back to its first flat condition. The experiment was repeated three times. The second time a small ball was used to indicate the sheet transformation of the gauze by its navigation on the surface. The third time the sheet was deformed in a specific pattern, symmetrically, to attest our hypothesis that the way of its restoration can be predicted if the first shape of deformation is controlled (See Exhibits P- Q).
These experiments served as a first prototype for our final project and helped us organize our grid of wires. They were also useful in examining the type of the wires connection to the fabric and in deciding to have them free-floating in a frame instead of selecting fixed points, as we did in the previous experiment. (Please see Exhibit 7 in Video Appendix)
Second Prototype -3D Selective zone heating (single circuit SMW grid attached to synthetic membrane)
The nickel-titanium alloy (Nitinol) wires (.0297” d.) were once again pre-set in the austenite state to be linear. Eight 8” long wires were configured in a grid pattern and adhered to a polyurethane membrane approximately 9” wide by 9” long. The corners of the membrane were attached to a cardboard frame with elastic bands. Electrical wiring was installed to provide one circuit to the shape memory wire grid. (See Exhibit R)
More precisely, the poly flat assembly was deformed to provide radiuses in the Z-axis direction. A ball was employed to show more effectively the change in the surface planes. The electric circuit was powered and attached to a specific bent of the surface. The effected bend went then back to its straight shape, influencing the surrounding, and the ball shifted position. (Please see Exhibit 8 in Video Appendix)
The project was successful in that it demonstrated that the shape memory wire grid could be pre-circuited to selectively apply heat to a desired action. This prototype was the cornerstone for us in order to move to a more complicated system with several points of activation, which could provide a bigger variety of both visual and kinesthetic effects.
Final Experiment- 3D Selective zone heating (multi-circuited SMW grid attached to dichroic membrane)
For the final project, the nickel-titanium alloy (Nitinol) wires (.0297” d.) were again pre-set in the austenite state to be linear. Eight 1ft long wires were configured in a grid pattern and adhered to a dichroic membrane 18” wide by 18” long. The corners of the membrane were attached to a wooden frame with elastic bands. Electrically wiring was installed to provide 16 circuits to the shape memory wire grid. (See Exhibits S – U)
Specifically, the assembly was deformed to provide radiuses in the Z-axis direction. The electric circuit was powered and attached to 16 specific bents of the surface. Switches enabled the control of each point separately. The effected bends were meant to go back to their straight shape, influencing the vicinage, as it had happened to the previous experiment. (Please see Exhibit 9 in Video Appendix)
However, this project was not a complete success. The circuiting was complicated and in the cases where two or more points were activated at the same time, the voltage was divided between them reducing the power exerted to each one (connected in parallel). A series of technical problems was specified as responsible for the partial success of this prototype. Specifically, the membrane was stiff and improperly connected to the wires. Thus, it was soon not following the movement of the wires. The circuit wires, on the other hand, were very heavy and disabled the movement of the shape memory grid to which they were attached. Finally, the shape memory wires themselves should probably be stronger (have a bigger diameter) in order to support the motion of such a wide area.
In conclusion, we believe that, through the experience we gained by this prototype, the knowledge for a successful future model lies in specific modifications. These modifications include: a lighter and flexible membrane properly attached to the shape memory grid, a lighter and shorter in length circuit system, a higher voltage (or a non-parallel circuit), slightly thicker SMW for greater force.
CONCLUSIONS AND FUTURE APPLICATIONS
Being aware of the numerous complicated variables inherent in shape memory materials, we understand that our research provides only an introduction to the possibilities of these alloys. Foremost is the result that changing even a small variable can significantly influence the whole behavior of the material. A small alteration can produce a great effect. This can lead us to a variety of applications.
By focusing on the 2D and 3D concept we came up with different inspirations for future experimentation, as well as applications. In two dimensions we envisage an interactive graphic application with emphasis on the visual effect. A new cursive font could be derived from interesting “play” with shape memory wires. Specific letters could be created by the wire itself and change from one form to another by heating it in specific zones.
As far as the 3D field is concerned, future applications prove to be more abstract and vague. SMW could be used as an armature for other applications instead of being the end product. They could be seen as a means to control something over-imposed or differently related to it. A thorough analysis of the curvatures could lead to a full control of the components connected to the wires (i.e. manipulation of light reflected from the surface).
Finally, it is crucial to take into account that each material has unique properties for exploitation. The high cost, low strength or slow reaction SMW may have, worked for a long time as impediments in the use of them in the architectural environment. However, we believe it is up to the architect to study their properties more precisely and use them wisely – by accepting the differences they imply, take advantage of them and respect the smaller scale they introduce to the design by their dimensions. These materials should not be used as substitutes to replace conventional materials, but as something unique with great potential and influences even in the whole architectural thinking.
© 2006 Dido Tsigaridi & Mikael Powell
VIDEO APPENDIX
Exhibit 1- Uniform heating of shape memory wire
Exhibit 2 - Shape Memory wire electric pistons- researching voltage to reaction time
Exhibit 3 - 2D Selective zone heating – Mode I - Graphically charting path of the ends and intermediate points with fixed end point.
Exhibit 4 - 2D Selective zone heating – Mode II -Graphically charting path of the ends and intermediate points with fixed center point.
Exhibit 5 - Re-Set Capabilities - Pistons can be alternately activated to reset the action.
Exhibit 6 - Experiment 5 - Re-Set Capabilities – Counter-balance to reset the action.
Exhibit 7 - First Prototype - 3D Uniform heating (SMW grid woven through cotton fabric)
Exhibit 8 - Second Prototype -3D Selective zone heating (single circuit SMW grid attached to synthetic membrane)
Exhibit 9 - Final Experiment- 3D Selective zone heating (multi-circuited SMW grid attached to dichroic membrane)
Exhibit 10 – Experiment on the way heat application affects reaction speed.
[1] Addington, M., Schodek, D., Smart Materials and Technologies, Architectural Press, Oxford, 2005, pp.16-17.
[2]
[3] Ibid.
[4] Otsuka, K., Wayman, C.M., Shape Menory Materials, Cambridge University Press, Cambridge, 1998.
[5] For commercial exploitation, a third metal is usually added to the binary NiTi alloy to improve its properties. “Up to 30% of the nickel can be replaced by copper without loss of the shape memory effect. The effect of the copper addition is to reduce the hysteresis to about 15C and also make the transformation temperature less sensitive to changes of the nickel content.”
[6]
[7] Educational Innovations Inc. claim that the martensite structure has “24 different variants to carry out this transformation” and, as a result, the material can be deformed in nearly any direction.
[8] The tables come from measurements on FlexinolTM wires. FlexinolTM is a trade name for shape memory actuator wires made of Nickel-Titanium. Gilbertson, R.G., Muscle Wires: Project Book, Mondo-Tronics, San Anselmo, 1994.
[9] Ditullio, Michael & Tsigaridi, Dido for Advanced Materials class, November 2005.
[10] The hysteresis effect – the fact that heating and cooling transformations do not overlap – is also related to fatigue.
[11] The amount of this shape change is said to be significantly less than the obtained with one-way shape memory and very little stress can be exerted by the alloy as it tries to assume its low-temperature shape. However, the heating shape change can still exert very high forces.
[12] Ditullio, Michael & Tsigaridi, Dido for Advanced Materials class, November 2005.
(COPYRIGHT © 2006 POWELL/TSIGARIDI. All Rights Reserved)
No comments:
Post a Comment